|
|
|
|
CVD has been a technique utilized since the 1960's as a means to apply protective coatings onto many substrates for wear and oxidation betterment. The photo to the right illustrates an early example of a TiC (Titanium Carbide) coated Tungsten Carbide Cobalt "hard-metal" tool.
The coating applied here was deposited using the Titanium Tetrachloride disproptionation reaction. TiCl4 was carried into a high temperature retort (1800 deg. F) and the metal chloride was converted to an unstable sub-chloride (TiCl) which reacted with the carbon in the substrate to form TiC (leaving behind a carbon deficient zone in the substrate).
Cutting Tool Coatings
Within a very short period of time, several companies had introduced coatings of their own to compete with Metallgesellschaft. This included companies such as Kennametal, Sandvik, Carboloy, Teledyne Firth-Sterling, etc. to name a few. By 1978, approximately 50% of all tungsten carbide indexable cutting tools were being coated.
|
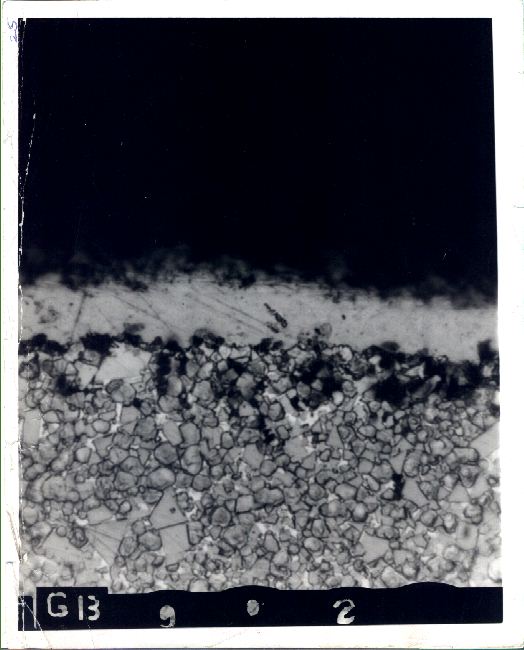 |
Advanced Metallurgical Coatings Capabilities
Having been involved in all aspects of CVD since 1969 at tool production companies such as Kennametal and Newcomer Products, the equipment producer Ti-Coating and the aerospace coating company, Chromalloy prior to the formation of "AMC", we can provide the technical information as to "how to" process parts as well as "how to" design and build the equipment.
Consulting Services / Equipment
If you need assistance in processing tool coatings such as TiC, TiCN, TiN, TiB2, Al2O3, ZrC, ZrO2 as processed by CVD we can assist in all aspects of these coatings.
amc email address
Oxidation Protection
The coating depicted here is a CVD coating of Silicon Carbide deposited onto carbon-carbon. Typically, these materials will burn up in air when subjected to high use temperatures - but with the silicon carbide deposited as a protective coating it can survive up to approximately 2800 deg. F. Cycle life however is dependent upon factors such as thickness as well as CTE = coefficient of thermal expansion. In some cases with a poor CTE match, a glass former may be used as an underlayer.
AMC-Diffusion Coatings
|
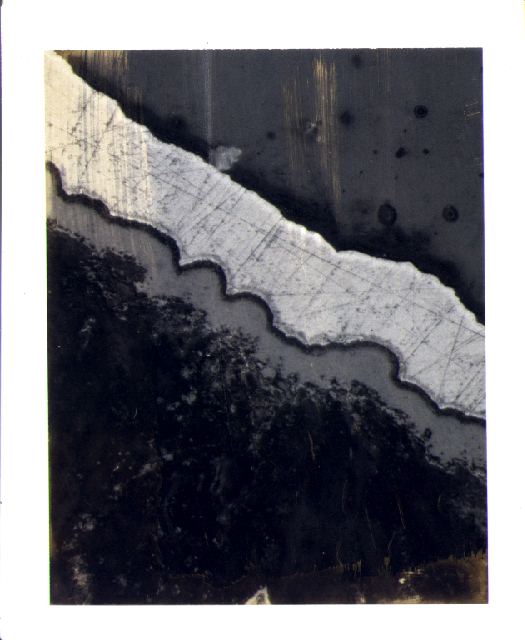 |
|